Precision Pipe Extrusion Line
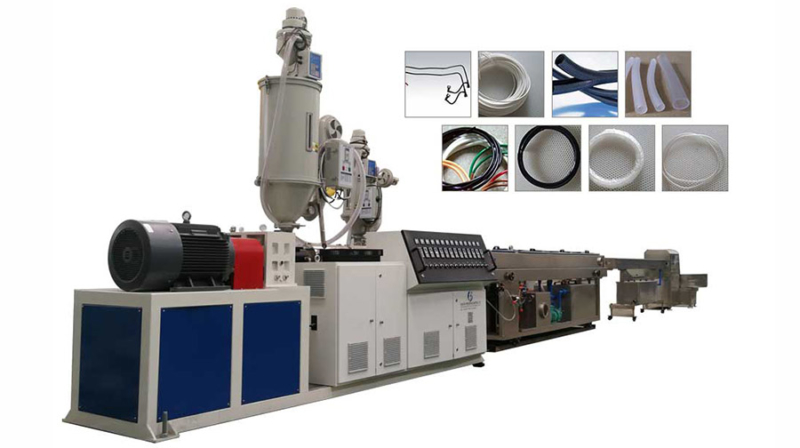
1. “SXG” series precision pipe extrusion line is a new equipment that launched by GangSu Machinery and specially used for producing various types of precision small diameter pipe , eg automotive piping systems, medical pipe, pneumatic pipe, multi-layer nylon PA fuel pipe, multi-layer composite pipe, High-pressure liquid pipe, precision communication cable, packaging beverage or cleaning containers straw.
2. After continuous development and promotion, at present our company has officially launched a new product “SGX” system precision pipe extrusion line, which is dedicated to a variety of precision small diameter pipes. Its stable performance and mature technology have won wide affirmation of the industry’s high-end customers. This line has adopted a unique “accurate control of weak vacuum” and “high pressure volumetric extrusion” technology. It has improved the shortage of traditional progress which cannot balance the extrusion speed and precision control, especially when it is applied in PA/PU/POM and fluorine plastic pipe. It can greatly improve the customer’s value-in-use value of machines and brings significant cost saving effect. This new product can meet the high precision extrusion control of the pipe while achieving the desired production efficiency and the whole line speed can reach up to 300m/min.
Layout:
Raw Material Mixing → Vacuum Loading → Drying → Single Screw Extruder → Mould → Vacuum Calibration Tank → Soaking Cooling Tank → High Speed Haul-Off → Fly Knife Cutter → Completed Product Inspection & Packaging